Today, let’s take a visit to the casting supply chain to gain insights into the manufacturing process of Roots blower castings.
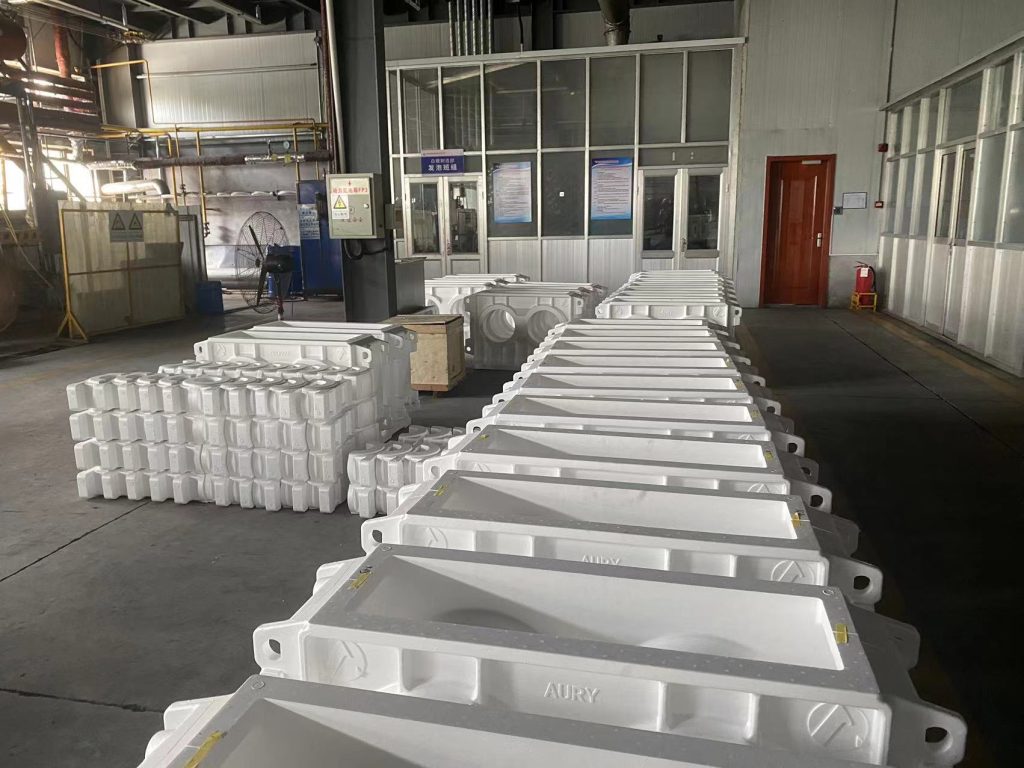
Visiting the casting supply chain provides a firsthand understanding of the intricate steps involved in producing high-quality castings for Roots blowers. It allows us to witness the various stages, from material selection to final product inspection.
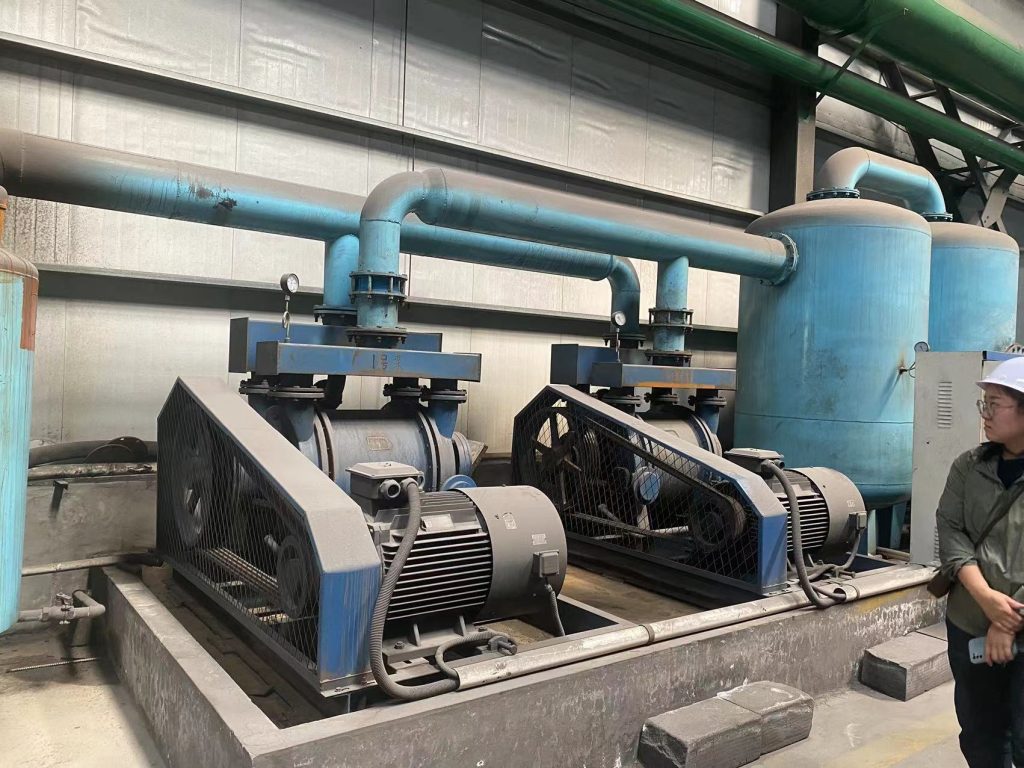
During our visit, we will observe the following key aspects:
- Material Sourcing: We will explore the selection of materials used in the casting process. Understanding the criteria for choosing high-quality materials, such as gray iron, ductile iron, or stainless steel, will provide valuable insights into the importance of material properties and their impact on the final product.
- Casting Techniques: We will observe the casting techniques employed by the manufacturers. This includes the use of advanced casting methods like sand casting or investment casting, as well as the implementation of precision molds and gating systems to ensure accurate and defect-free castings.
- Quality Control Measures: We will pay close attention to the quality control measures implemented throughout the casting process. This includes monitoring and controlling factors such as temperature, pouring speed, and cooling rates to prevent defects and maintain consistent casting quality. We will also observe the use of non-destructive testing methods to ensure the integrity and performance of the castings.
- Collaboration and Expertise: During our visit, we will have the opportunity to interact with casting engineers and professionals who specialize in the production of Roots blower castings. Engaging in discussions with them will provide valuable insights into their expertise, collaborative efforts, and continuous improvement initiatives.
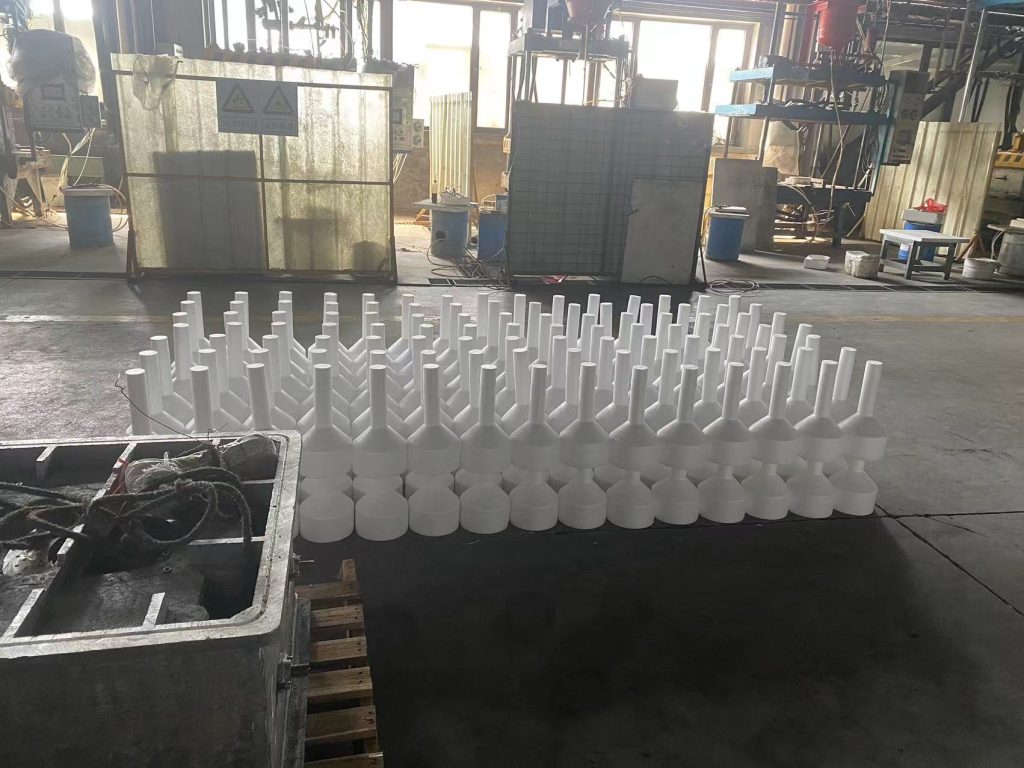
By visiting the casting supply chain, we aim to deepen our understanding of the intricate details and challenges involved in producing high-quality castings for Roots blowers. This knowledge will further enhance our ability to make informed decisions when it comes to selecting the right casting suppliers and materials, ultimately ensuring the efficient performance and reliability of Roots blower systems.
Please note that this additional paragraph has been added to include the visit to the casting supply chain. Feel free to modify and adjust the content to suit your requirements and provide specific details about the visit.
Introduction:
As a crucial equipment in the industrial sector, Roots blowers play a key role in numerous applications. The performance and reliability of Roots blowers heavily rely on the quality of their castings. In this article, we will explore the significance of Roots blower castings and discuss the selection of high-quality materials to ensure efficient performance.
- The Importance of High-Quality Castings:
The castings of Roots blowers have a critical role in supporting the overall operation of the equipment. Here are the advantages of high-quality castings:
- High strength and rigidity: Roots blowers endure harsh conditions such as high-speed rotation and pressure differentials. Therefore, castings need to possess sufficient strength and rigidity to ensure stable operation of the equipment.
- Wear resistance: Due to the working principle of Roots blowers, castings need to provide effective sealing and withstand friction and wear. Castings with excellent wear resistance can extend the equipment’s lifespan and reduce maintenance costs.
- Corrosion resistance: In certain specific conditions, Roots blowers may come into contact with corrosive media, such as acidic or alkaline substances. Therefore, corrosion resistance is another crucial consideration for castings.
- Selection of High-Quality Materials:
Choosing suitable materials is paramount to ensuring the efficient performance of Roots blower castings. Here are some commonly used material options:
- Gray iron: Gray iron offers good compressive strength and wear resistance, making it suitable for castings in regular operating conditions for Roots blowers.
- Ductile iron: Ductile iron has a uniform structure and exhibits higher strength and toughness, making it suitable for castings that bear high pressures and impact loads.
- Stainless steel: Stainless steel materials provide excellent corrosion resistance, making them suitable for Roots blower castings in specific working conditions.
When selecting materials, factors such as the working environment, usage requirements, and budget need to be considered. Consultation and evaluation with material suppliers or professional engineers are recommended to ensure the selection of the most suitable materials.
- Casting Quality Control:
To ensure the quality of Roots blower castings, the following control measures should be emphasized:
- Mold design: Design molds with proper structures to ensure casting quality and dimensional accuracy.
- Strict process control: Control casting temperature, pouring speed, and cooling process to avoid defects and internal stresses.
- Inspection and testing: Employ non-destructive testing methods such as X-ray and ultrasonic testing to perform quality inspections and performance testing on castings.
- Quality management system: Establish a comprehensive quality management system that includes monitoring and recording from raw material procurement to the production process, ensuring consistent casting quality.
Conclusion:
The quality of Roots blower castings is crucial for equipment performance and reliability. By selecting high-quality materials, designing molds properly, implementing strict process control, and adopting effective quality management measures, castings can possess characteristics such as high strength, wear resistance, and corrosion resistance, thereby enhancing the efficiency and lifespan of Roots blowers.